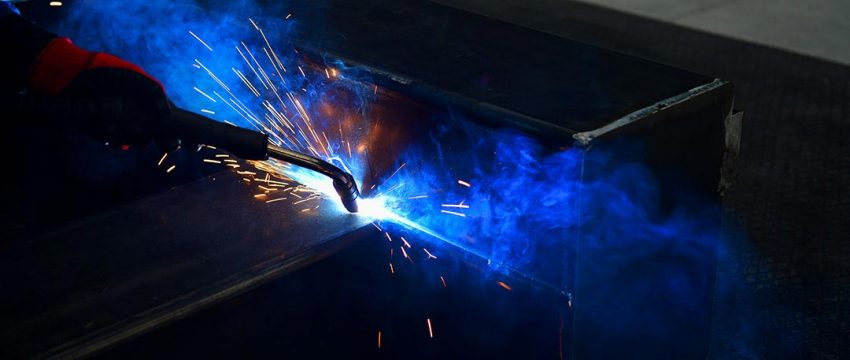
The success of narrow groove GMAW hinges on pinpoint accuracy.
Narrow groove gas metal arc welding (GMAW) has revolutionized the joining of heavy-section materials, offering efficiency and minimal distortion. This advanced technique utilizes a nearly square butt configuration with a groove width of about 13 mm, making it ideal for carbon and low-alloy steels. However, the success of this method hinges on precise electrode positioning to ensure proper fusion. Let’s explore some ingenious wire feeding approaches that have proven effective in industrial settings.
Tandem Wire Technique
One innovative method employs two wires with a controlled cast and separate contact tips. This tandem setup directs arcs towards each groove face, creating a series of overlapping fillet welds. The result is a strong, uniform joint that maximizes fusion and penetration.
Mechanical Oscillation Approaches
Several techniques have been developed to achieve a weaving motion of the arc across the groove:
- Contact Tip Movement: While theoretically possible, oscillating the contact tip mechanically across the narrow groove has proven impractical due to space constraints.
- Angled Contact Tip: A more viable option involves using a contact tip bent at approximately 15 degrees. As welding progresses, the tip twists side to side, imparting a weaving motion to the arc.
Waved Electrode Innovation
A sophisticated approach utilizes a unique wire feeding mechanism. The electrode is continuously deformed into a wave shape by a flapper plate and rotating feed rollers. Although nearly straightened while passing through the contact tip, the wire recovers its waviness beyond, resulting in an oscillating arc within the narrow groove.
Twist Electrode Technique
This clever method improves groove face penetration without moving the contact tip. Two intertwined wires are fed into the groove, generating arcs from their tips. The twist causes a continuous rotational movement of the arcs, enhancing penetration without the need for a separate weaving device.
Large Diameter Electrode Alternative
For those seeking a simpler setup, an alternative involves feeding a larger diameter electrode (2.4-3.2 mm) directly into the groove center. This technique uses a contact tip positioned above the plate surface, reducing the risk of arcing between the tip and the workpiece. While it allows for the use of standard welding equipment, it has limitations in terms of thickness potential and is typically restricted to flat-position welding.
Considerations and Challenges
While these innovative wire feeding methods offer significant advantages, they often require specialized equipment. The choice of technique depends on factors such as:
- Joint thickness
- Material properties
- Welding position
- Available equipment
- Operator skill level
It’s crucial to note that regardless of the chosen method, accurate wire placement remains critical for achieving high-quality welds in narrow groove GMAW applications.
Conclusion
The evolution of wire feeding techniques for narrow groove GMAW demonstrates the industry’s commitment to improving welding efficiency and quality. From tandem wire setups to waved electrodes and twist electrode innovations, these methods offer welders a range of options to tackle challenging heavy-section joints. As technology continues to advance, we can expect further refinements and novel approaches to emerge, pushing the boundaries of what’s possible in narrow groove welding applications.
By carefully selecting the most appropriate wire feeding technique and ensuring precise execution, fabricators can harness the full potential of narrow groove GMAW to produce high-integrity welds with minimal distortion in heavy-section materials.