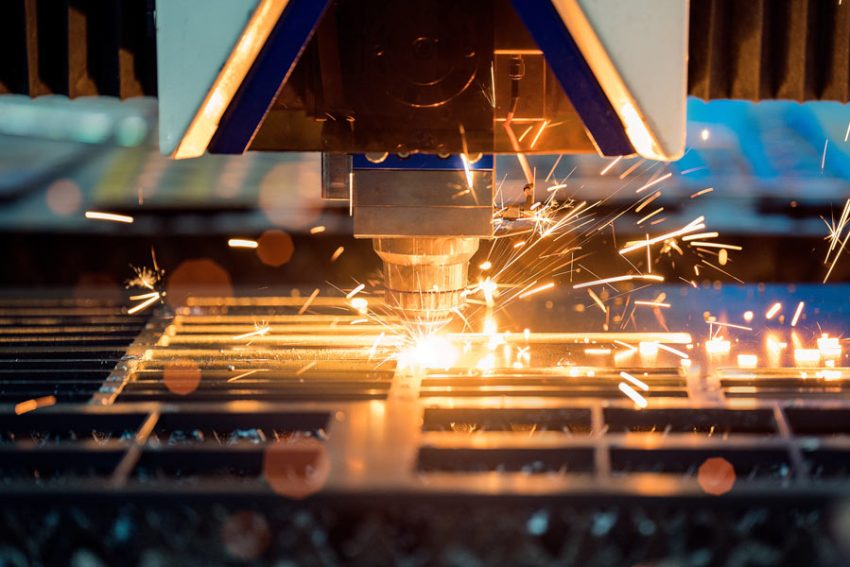
In the world of metal fabrication, two cutting methods stand out: fiber laser and plasma cutting. While both technologies have their merits, understanding their unique characteristics is crucial for selecting the best option for your business needs. So, which method will give you the edge in your projects?
Cut Quality Comparison
- Precision and Angularity
Fiber laser cutting excels in producing narrow, precise cuts with low angularity. This makes it ideal for cutting fine features, especially in thinner materials. Fiber lasers typically achieve ISO 9013 range 1-2 cuts, indicating superior cut angularity.
- Surface Finish and Dross Formation
Plasma cutting has evolved significantly, now offering smooth and straight cut edges with minimal oxide layers and dross. High-definition plasma usually yields ISO range 2-4 cuts, rivaling fiber laser quality for most applications. However, fiber laser can sometimes produce rougher edges with more dross, particularly in thicker metals.
- Kerf Width and Part Removal
Fiber lasers create a narrower kerf, allowing for better plate utilization and fine-feature capability. However, this can make part removal challenging in thicker plates. Plasma cutting, with its wider kerf, often facilitates easier part removal from the skeleton.
Material Versatility
-
Handling Imperfect Surfaces
Plasma cutting shines when dealing with imperfect materials. It can easily cut through rusty, painted, or coated surfaces without requiring pre-treatment. Fiber lasers, on the other hand, may struggle with such materials, often necessitating additional preparation steps.
-
Material Storage and Handling
Fiber laser cutting may require indoor material storage to maintain optimal cutting conditions, potentially increasing costs and consuming shop floor space. Plasma cutting is more forgiving, allowing for outdoor storage and handling of various material conditions.
Cost Considerations
Fiber laser systems typically cost two to five times more than comparable plasma machines, resulting in longer payback periods. Plasma systems often recover capital expenses within two years or less.
While fiber lasers are more efficient for cutting thin materials, plasma holds the advantage in thicker metals, offering greater productivity and lower operating costs. The cost difference is primarily driven by electricity and gas consumption.
Maintenance and Durability
-
System Complexity
Fiber laser systems have fewer consumable parts but higher maintenance costs due to complex cutting heads and motion control components. They may require repair by authorized service centers only.
-
Environmental Sensitivity
Fiber lasers are more sensitive to dirty shop environments, as contaminants can affect optical components and precision drives. Regular cleaning and maintenance are crucial for optimal performance.
-
Robustness
Plasma systems are generally more robust and forgiving in harsh environments. They allow for simple, in-house maintenance and are well-suited for industrial settings.
Conclusion
When choosing between fiber laser and plasma cutting, consider your specific project requirements, including material types, thicknesses, production volumes, and desired finish quality. Fiber laser cutting is typically preferred for thin to medium-thickness materials requiring high precision, while plasma cutting is more suitable for thicker materials and applications prioritizing cost-effectiveness and cutting speed.
Ultimately, the best choice depends on your unique needs, budget, and production requirements. Consulting with industry experts can help you make an informed decision that aligns with your business goals and fabrication needs.