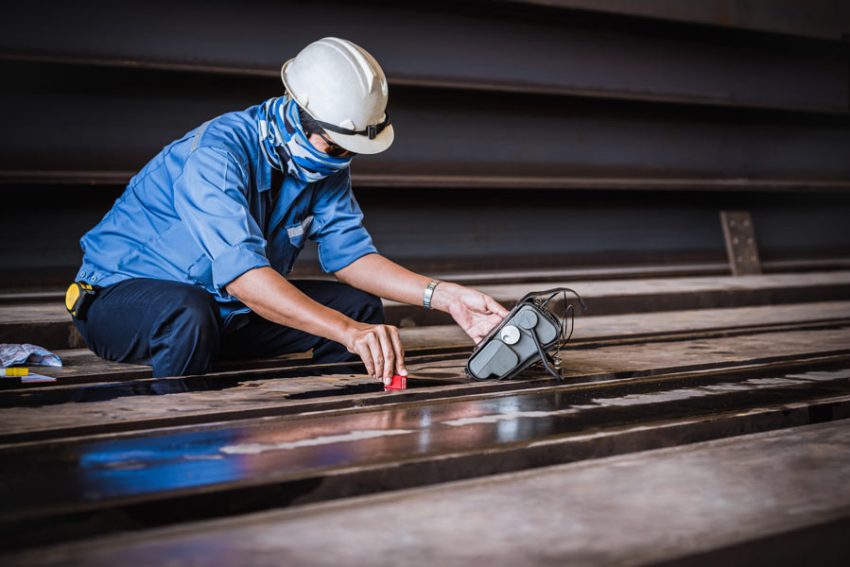
Weld cracking is a critical issue in metal fabrication that can lead to catastrophic failures in structures and components. As the most severe form of discontinuity, cracks are characterized by their sharp tips and high ratio of length and width to the displacement of the opening. They occur when localized stresses exceed the ultimate strength of the metal, often associated with stress amplification near discontinuities or mechanical notches.
Types of Weld Cracks
-
Hot Cracks
Hot cracks develop at elevated temperatures, typically during the solidification of the weld metal. These cracks propagate between the grains (intergranular) and are commonly found in metals with high coefficients of thermal expansion, such as austenitic stainless steel. Hot cracks can be particularly problematic as they may serve as initiation points for other types of cracks, potentially compromising the entire weld integrity.
-
Cold Cracks
Cold cracks, also known as delayed cracks, form after the solidification of a fusion weld as a result of residual stresses. Often associated with hydrogen embrittlement in steel, these cracks can propagate both between the grains (intergranular) and through the grains (transgranular). Cold cracks are particularly insidious as they may not appear immediately after welding, making detection and prevention challenging.
Common Crack Locations
Cracks can occur in various locations within a weldment, each with its own set of causes and characteristics. Some of the most common crack locations include:
- Crater cracks: Shallow hot cracks formed by improper termination of a welding arc, often star-shaped and limited to the crater edge.
- Face cracks: Longitudinal cracks on the weld’s exterior surface, caused by excessive concavity, insufficient reinforcement, or rapid cooling.
- HAZ or underbead cracks: Cold cracks in the heat-affected zone (HAZ), usually short and discontinuous, difficult to detect visually.
- Longitudinal cracks: Occurring within the weld metal, parallel to the weld axis, often due to high restraint or shrinkage stress.
- Root cracks: Running along the weld root or surface, these can be hot or cold cracks caused by incomplete penetration or contamination.
- Toe cracks: Cold cracks initiating at the weld toe, often due to thermal shrinkage strains in an embrittled HAZ.
- Transverse cracks: Running perpendicular to the weld axis, these cracks result from longitudinal shrinkage strains in low-ductility weld metal.
Understanding the location and characteristics of these cracks is essential for proper inspection, diagnosis, and prevention strategies.
Causes of Weld Cracking
The causes of weld cracking are multifaceted, involving a complex interplay of metallurgical, mechanical, and environmental factors. Localized stress is a primary cause, occurring when stresses in a specific area exceed the metal’s ultimate strength. This can be exacerbated by the presence of stress concentrators such as discontinuities or design features.
Shrinkage is another significant factor, as all welds experience some degree of shrinkage during cooling. If the joint or HAZ cannot accommodate these shrinkage stresses through plastic deformation, high stresses develop, potentially leading to cracking.
The chemical composition of both the base metal and weld metal plays a crucial role in crack susceptibility. Certain elements can increase hardenability, potentially leading to brittle microstructures in the HAZ that are more prone to cracking. The hardness and brittleness of the weld metal or HAZ after cooling also significantly affect crack susceptibility, as harder or more brittle metals are less able to withstand stress concentrations through localized yielding.
Prevention and Remedies
Preventing weld cracking requires a comprehensive approach that addresses the root causes of cracking. For weld metal cracking, several strategies can be employed:
- Modify electrode manipulation or electrical conditions to improve weld face contour or composition
- Select more ductile filler metals to enhance crack resistance
- Increase weld pass thickness by decreasing welding speed
- Use preheat to reduce thermal stresses
- Implement low-hydrogen welding procedures
- Sequence welds to balance shrinkage stresses
HAZ cracking prevention focuses on controlling the metallurgical response of the base metal to the weld thermal cycle. This can be achieved by:
- Managing cooling rates through preheat and heat input control
- Considering base metal composition and hardenability when selecting welding parameters
- Minimizing joint restraint where possible
Base metal cracking, particularly hydrogen-induced cracking, can be mitigated through:
- Using low-hydrogen welding processes
- Applying thermal treatments to promote hydrogen diffusion
- Developing welding procedures that result in low welding stresses
Conclusion
Weld cracking remains a significant challenge in metal fabrication, influenced by a wide array of factors including material properties, welding techniques, and environmental conditions. By understanding these factors and implementing appropriate preventive measures, welders and engineers can significantly reduce the risk of weld cracking. This not only improves the integrity of welded structures but also enhances their longevity and safety.
Continuous education, adherence to best practices, and ongoing research into new prevention techniques are essential for maintaining high standards in welding quality and structural integrity.