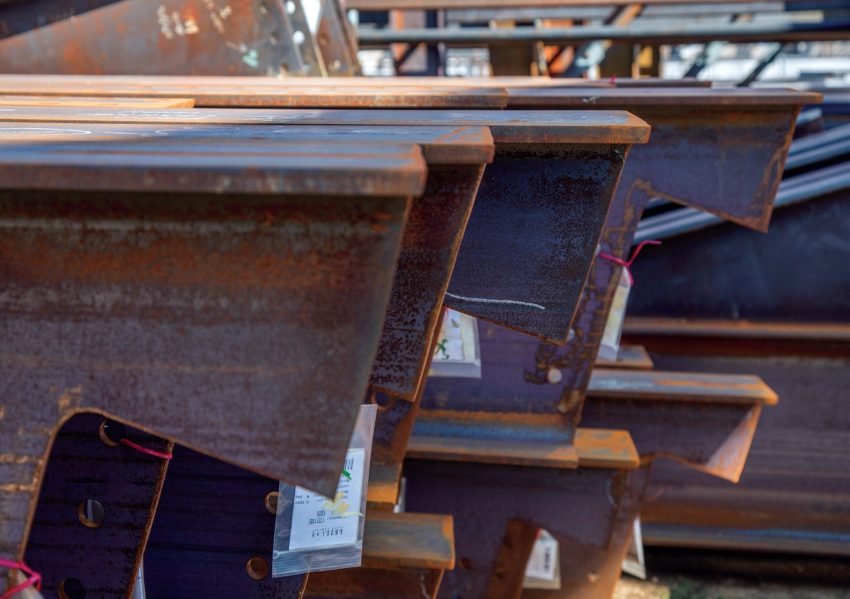
Welding wires rich in deoxidizing elements can penetrate through material coatings and contaminants
Demanding material surface conditions are frequently encountered in welding applications. In an effort to reduce costs on competitive projects, fabrication shops, and construction firms often omit material cleaning steps from their processes. Whether the material carries rust, mill scale, coatings, or other impurities, the common approach is to “just weld over it.” In these situations, selecting the appropriate filler wire for the base material’s surface state can help mitigate quality issues and enhance weld outcomes.
Prevalent Surface Conditions
Some of the most widespread material surface conditions faced in welding are mill scale, galvanized coatings, oil residues, and rust. These conditions may arise from treatments applied during material manufacturing or from the storage environment of the products. Removing such coatings and contaminants requires time and adds expense, so many operations forgo the cleaning process. Instead, welding is performed directly over the material’s surface condition, which can introduce challenges and impact weld quality.
While thorough base material cleaning is always recommended, in cases where this is not feasible or practical, choosing the right filler wire can improve results when welding over these surface conditions.
Welding Over Mill Scale
Mill scale is an oxide layer that forms on metal during hot rolling in the manufacturing process. Cold rolling eliminates mill scale formation but increases production costs, so many operations opt for hot-rolled over cold-rolled material. The mill scale layer can also be blasted off prior to welding. One major drawback of welding over mill scale is the need for a much slower travel speed, sometimes half the speed used for clean, prepped base material. The slow speed is necessary to burn off the mill scale layer with the arc. Welding too quickly over mill scale causes an erratic weld pool and inconsistent or wavy weld beads. More spatter is also produced compared to welding clean metal.
When choosing a filler wire to tackle mill scale, a flux cored wire can be advantageous. Flux cored wires typically contain the highest levels of deoxidizers, which help float impurities to the surface. Good flux cored wires for welding mill scale are AWS classes E71T-1C/M and E71T-9C/M, providing superior weldability compared to other flux cored wires.
Metal cored wires, such as AWS E70C-6M, are also suitable choices due to their high silicon content and excellent deoxidizing and impurity-gathering capabilities, allowing them to perform well on dirtier materials.
Using a shielding gas blend like 90% argon and 10% carbon dioxide produces a hotter arc beneficial for welding steel with mill scale, rust, or primer coatings. The higher temperature helps burn away coatings and rust faster. Slightly increasing the welding voltage can provide similar benefits.
Welding Galvanized Steel
Galvanized base metals are ubiquitous in many welding applications. Galvanizing involves dipping or electroplating to apply a coating that prevents rust and oxide formation on the metal. Thicker coatings offer better protection but are more challenging to weld over. Welding galvanized steel necessitates slower travel speeds and can cause porosity and weld cracking. Avoiding galvanizing before welding and instead applying the coating after welding is preferred to circumvent these issues. If high residual stresses remain after welding, liquid metal embrittlement and cracking in the weld or heat-affected zone may occur during subsequent hot-dip galvanizing.
For applications requiring welding on galvanized steel, certain filler metals perform better on galvanized and coated materials. A flux cored wire with AWS E71T-11 classification works well on coated steels due to added aluminum and other deoxidizers that help reduce impurities and cracking.
Welding Over Rust
Rust is another common surface condition encountered. Unlike mill scale, which forms during manufacturing, rust develops when metal is exposed to the atmosphere. Moisture and humidity can accelerate rusting, so proper material storage is crucial.
Rust exhibits lower electrical conductivity than steel, making it harder to establish a stable arc on heavily rusted material. Thicker rust layers increase welding difficulty. Welding over rust can cause porosity and excessive spatter.
To weld through rust, look for flux-cored and metal cored wires with high deoxidizer levels. For welding A36 steel, AWS E71T-1C/M and E71T-9C/M flux cored wires are good options. For metal cored wires, the AWS E70C-6M classification is suitable.
Oil-Coated Materials
Many plates and metal components enter the welding process with oil coatings, often residual lubricants from cutting operations. There is little justification for welding over oil since removing it from metal parts is a much faster and easier process compared to dealing with the other surface conditions listed. Simply use acetone and a rag to wipe the oil from the weld joint and surrounding area.
Optimizing Performance
When welding over dirty or coated materials, thorough cleaning and part preparation are ideal. However, when this is not possible due to time or cost constraints, choose a filler wire with a high deoxidizer content to penetrate through coatings or mill scale layers and deliver improved performance and results.
source: www.aws.org February 2023 Volume 102 Number 2 PG 21 “Material Conditions & Filler Metal Selection”