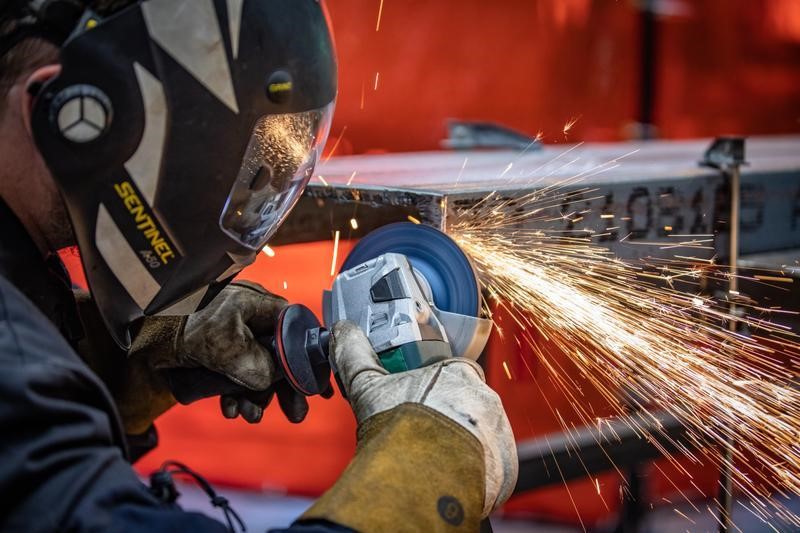
Metal grinding operations are inherently demanding. However, optimizing productivity can be achieved by choosing the appropriate abrasive product and tool for the specific application, and employing proper usage techniques.
When tasks like weld blending, bevel preparation, or aggressive material removal to precise dimensions are required, portable grinding wheels represent an efficient solution. However, extracting peak performance from grinding wheels necessitates attention to several key factors. This article provides insights into grinding wheel options and tips for maximizing productivity when utilizing these wheels in manufacturing or fabrication environments.
Advantages of Portable Grinding Wheels
Portable grinding wheels, typically used with handheld right-angle grinders, offer versatility and portability since they can be brought to the workpiece. They also possess the capability for rapid material removal rates. This characteristic enables operations to maintain focus on productivity and transition more quickly to subsequent jobs.
Type 27 grinding wheels, featuring a flat grinding face with a depressed center, are the most prevalent portable abrasive grinding wheel configuration and are commonly 1/4 inch thick. Traditionally, wheels designed for extended life tend to exhibit slower cutting speeds, while those prioritizing faster cutting rates have reduced lifespans. However, some grinding wheel products on the market are specially formulated to sustain high cutting speeds while also delivering longer service lives. This capability helps operations increase uptime and reduce wheel changeover frequency, saving time and costs. Another common choice for industrial use is the Type 27 combination wheel in a 1/8 inch thickness, with some versions capable of grinding, cutting, and notching for extreme versatility.
Grinding Wheel Options
To select the optimal grinding wheel, it is crucial to consider the application requirements, including the workpiece material, the tool being utilized, and the desired outcome — Fig. 1. Numerous factors differentiate wheel performance, such as the abrasive grain type, resin formulation, additives, and fiberglass reinforcement, all influencing results, wheel life, and cutting performance.
GRAINS: Some of the most prevalent grain options include the following. Aluminum oxide is an abrasive grain well-suited for steel, iron, and general metal applications, providing rapid initial cutting action. However, it tends to dull over time and lacks the sustained cut rate and longevity of certain other grains. Ceramic alumina grains offer self-sharpening benefits and consistent performance throughout their lifespan as fracturing continuously exposes fresh cutting edges. Some options employ microfracturing technology to expose even more sharp grain points. They deliver extended operating life under moderate pressures and are ideal for challenging materials like titanium, Inconel, or stainless steel. Silicon carbide is an exceptionally sharp and fast-cutting grain, albeit friable, so it lacks the toughness of other grains. It performs best on softer materials such as aluminum and is commonly used in products designed for stone, concrete, or ductile iron grinding. Zirconia alumina is a tough, self-sharpening grain suitable for a wide range of applications, including those requiring heavy pressures.
FIBERGLASS: The fiberglass within a grinding wheel provides the reinforcement that holds the abrasive structure together, contributing rigidity and impacting grinding performance. Fiberglass is available in different weaves and thicknesses. Seek out combination wheels incorporating triple layers of reinforced fiberglass, which offers additional support and strength for aggressive stock removal across multiple applications.
BONDS: The bond is the material that causes the abrasive mixture to adhere and maintain its intended shape. Bonds are composed of various materials like dry and wet resins along with additives. A grinding wheel’s bond can range from hard to soft consistencies. Generally, harder bonds prolong wheel life when operated and maintained correctly, while softer bonds facilitate smoother grinding and more rapid exposure of fresh cutting grains. Selecting the appropriate bond level for a given application and material can help balance performance and longevity while also enhancing control and mitigating chatter and operator fatigue.
Tips for Improving Productivity
Maximizing productivity in the demanding task of grinding hinges on several key factors. Here are seven tips to help optimize grinding wheel efficiency:
TIP 1: Choose tools carefully
Tool power plays a significant role in grinding wheel performance. If the tool lacks sufficient power or torque, the operator will be unable to fully realize the wheel’s designed capabilities. For example, grinding wheels containing ceramic alumina grains require higher-powered tools to take full advantage of the self-sharpening grain benefits. Even a seemingly minor factor like the extension cord gauge can impact wheel performance. Depending on length, using a heavy-duty 10 or 12-gauge extension cord instead of a lighter 16-gauge cord will notably affect the wheel’s performance and heat generation in the cord itself. Always avoid connecting multiple cords in series.
TIP 2: Start with a pull motion
With a new grinding wheel, initiate grinding using a pull motion rather than a push for the first few strokes. This approach helps condition the wheel’s edge, prevents initial gouging of the workpiece, and allows the operator to become accustomed to the wheel’s performance characteristics. If the application permits, use long, smooth sweeping motions and avoid short, choppy strokes, which promote consistent material removal in the work area and reduce the risk of digging into the workpiece and creating rework.
TIP 3: Avoid dwelling
Maintaining steady, consistent wheel movements is crucial; dwelling or lingering in one spot should be avoided — Fig. 2. Otherwise, heat will rapidly build up, potentially causing discoloration on high-value workpieces. Dwelling can also result in excessive localized material removal, likely necessitating costly rework.
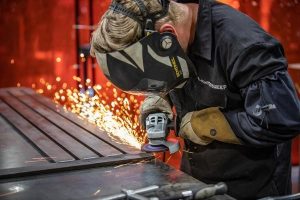
Fig. 2 — Maintaining steady wheel motion and avoiding dwelling in one area is important when grinding.
TIP 4: Use proper pressure and orientation
While operators may assume that applying greater pressure will accelerate the grinding process, excessive force on a grinding wheel can lead to problems and increase operator fatigue. Instead, use moderate pressure and allow the wheel to do the work — Fig. 3. The orientation of the wheel relative to the workpiece is also critical for optimal performance and productivity. The typical ideal angle for grinding wheel use is between 25 and 35 degrees, though shallower or steeper angles may be safely used for certain applications, albeit with reduced wheel life and efficiency. Additionally, not all 1/8-inch combination wheels are created equal; some are designed specifically for cutting and grinding, while others are intended for vertical use only. Ensure the usage technique aligns with the wheel’s instructions; if it specifies vertical use only, do not grind with the wheel’s face.
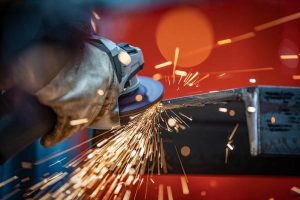
Fig. 3 — Apply moderate pressure and maintain the proper wheel orientation for optimal productivity.
TIP 5: Optimize wheel life
Utilizing a grinding wheel throughout its full usable life helps operations minimize wheel costs and the downtime associated with frequent wheel changeovers, thereby improving overall uptime and productivity. Take advantage of technologies that help extend wheel life. For instance, Weiler’s Tiger® 2.0 cutting, grinding, and combo wheels feature a patented Optimum Use Line, a visual indicator that assists operators in safely using the wheel to its maximum service life.
TIP 6: Maintain a focus on safety
Adhering to basic safety practices is essential. Ensure the maximum RPM rating on the grinding wheel exceeds the maximum RPM rating of the tool itself. Also, verify that the wheel fits beneath the installed tool guard and keep the guard in place during use. Edge chipping or wheel breakage can pose serious safety hazards if fragments dislodge during operation. The Tiger 2.0 wheels incorporate anti-chip technology to extend life and minimize the potential for edge chipping or breakage, allowing the wheel to wear down smoothly. Additionally, QR codes on the wheels provide operators with instant access to safety information — Fig. 4.
TIP 7: Consider the application
One of the first steps in selecting the right grinding wheel is to consider the specific job at hand. Specialized wheel designs and formulations are available to cater to many different applications and materials. For example, in multi-pass welding operations, grinding often follows immediately after the root pass, when the weld is still very hot. In such cases, look for grinding wheels engineered to perform effectively on hot welds, minimizing issues like chatter and glazing. Foundry applications represent another highly specialized environment requiring wheels designed explicitly for those demanding conditions. Foundry grinding frequently involves hard-to-grind materials and powerful tools, necessitating wheels capable of withstanding heavy pressures and high torque loads to prevent premature edge failures. Furthermore, to avoid contaminating sensitive materials like aluminum and stainless steel during grinding, select contaminant-free wheels specifically engineered for use on those alloys. Aluminum, being a softer metal with a lower melting point than steel, requires wheels formulated to break down and avoid loading up with aluminum to maintain high productivity levels.
Maximizing Grinding Wheel Efficiency
To enhance safety, comfort, and productivity during demanding grinding tasks, it is crucial to consider multiple factors, such as choosing the appropriate product, employing proper techniques, and addressing the specific requirements of the application. Adhering to these recommended practices can contribute to increased efficiency when working with grinding wheels.
source: www.aws.org September 2023 Volume 102 Number 9 PG 26 “Tips for Optimizing Productivity w/ Grinding Wheels”