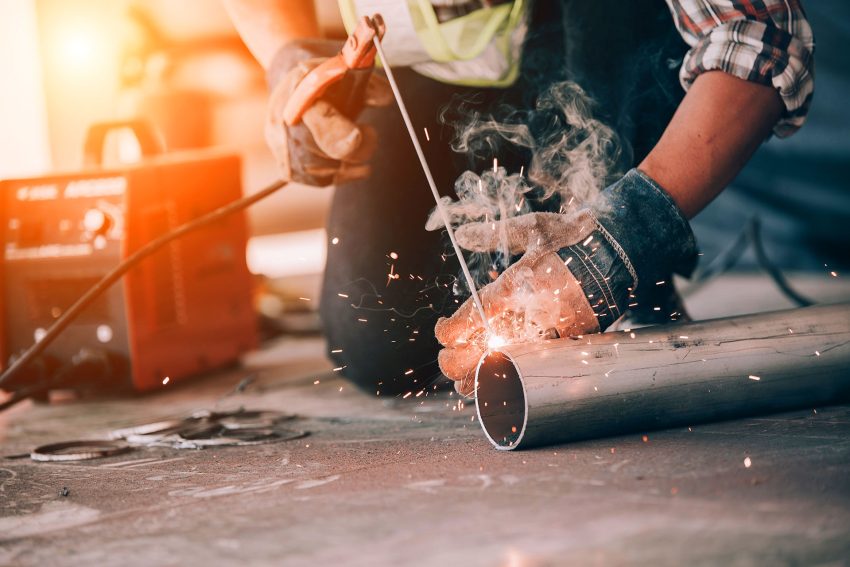
Contractors are constantly seeking ways to improve efficiency without compromising quality. Structural field welding is a critical area where significant improvements can be made, helping to overcome challenges such as supply chain disruptions and skilled labor shortages. By focusing on four key aspects of welding operations, contractors can boost productivity and maintain high standards on their job sites.
Choosing the Right Welding Process
While Shielded Metal Arc Welding (SMAW) has long been a staple in construction, it’s worth considering the advantages of Self-Shielded Flux Cored Arc Welding (FCAW-S) for larger multipass welds. FCAW-S offers higher deposition rates, with the potential to double or even triple the production compared to traditional 1/8-inch 7018 SMAW electrodes. This process also boasts greater deposition efficiency, typically achieving gains of 10% or more over SMAW due to reduced flux and stub loss.
The flexibility of FCAW-S is another significant advantage. Welders can start and stop at any time without wasting consumables, a feature that can lead to substantial cost savings over the course of a project. However, it’s important to note that SMAW still has its place in construction. Its mobility, reliability, and simple setup make it ideal for certain applications such as handrail and stair installation, as well as the erection of open web steel joists.
Selecting the Optimal Welding Wire
When it comes to structural welding with self-shielded flux cored wire, contractors have several options to consider. T-8 welding wire (classified as E71T-8) is a versatile choice suitable for all-position welding. It provides good impact toughness at low service temperatures and can be used for multipass welds of unlimited thickness. This wire operates using direct current electrode negative (DCEN) polarity.
For flat and horizontal welds, T-6 welding wire (E70T-6) is worth considering. Compared to T-8 wires, T-6 typically yields higher deposition rates and offers improved operating characteristics at very high amperages. It provides good penetration and generally produces good low-temperature impact toughness. Unlike T-8, T-6 welding wires are designed for welding using direct current electrode positive (DCEP) polarity.
T-11 welding wire (E70T-11) is another option, particularly popular for ancillary connections on thinner material. While it offers improved ease of use compared to T-8 wires and is available in a wider range of diameters, it does come with limitations. T-11 wires generally don’t offer the same level of toughness as the “seismic wires” (T-8 and T-6 wires tested to AWS D1.8 standards), and they have pass limitations in many fabrication codes.
Tackling Voltage Drop
Voltage drop is a common challenge in wire welding processes on construction sites. It occurs due to resistance in the current path, usually caused by the distance, configuration, and condition of the weld circuit. Even small changes in voltage can cause a welding power source to significantly adjust amperage when using constant voltage (CV) wire welding processes, affecting weld quality and consistency.
To minimize voltage drop, it’s crucial to watch out for excessive lead lengths, leads in poor condition, improper cable gauge for the application, and any impedance to the current flow in the connections. Regular inspection and maintenance of welding cables are essential, and damaged cables should be taken out of service promptly to avoid safety hazards.
Investing in technology that automatically adjusts for voltage drop can be a game-changer. For instance, cable length compensation (CLC™) technology on certain power sources automatically corrects the voltage by sensing and adjusting for the voltage drop. This ensures that the voltage set by operators is the voltage they get, even when working hundreds of feet away from the power source on a job site.
Prioritizing Jobsite Safety
A safer job site is ultimately more productive and profitable, as it reduces lost time due to accidents and injuries. When choosing welding equipment and technologies, look for solutions that contribute to a safer working environment. This can include quieter engine drives to reduce noise pollution, versatile helmets that provide protection for both welding and grinding, and equipment designed to reduce operator fatigue and the risk of slip, trip, and fall injuries.
Technologies that allow for remote parameter adjustment, such as ArcReach®, can significantly improve safety by reducing the need for welders to move back and forth across the job site. This not only increases efficiency but also decreases the risk of accidents in potentially hazardous construction environments.
Conclusion
By focusing on these four key areas – optimizing the welding process, selecting the right welding wire, addressing voltage drop, and prioritizing safety – construction contractors can significantly improve their welding operations. These strategies can help offset project slowdowns and labor challenges, ultimately leading to more efficient, high-quality project completions. As the industry continues to evolve, staying informed about the latest welding technologies and best practices will be crucial for maintaining a competitive edge in the construction market.
Source : November 2022 Volume 101 Number 11 PG 38 “Enhance Welding Efficiency on Construction Job sites”