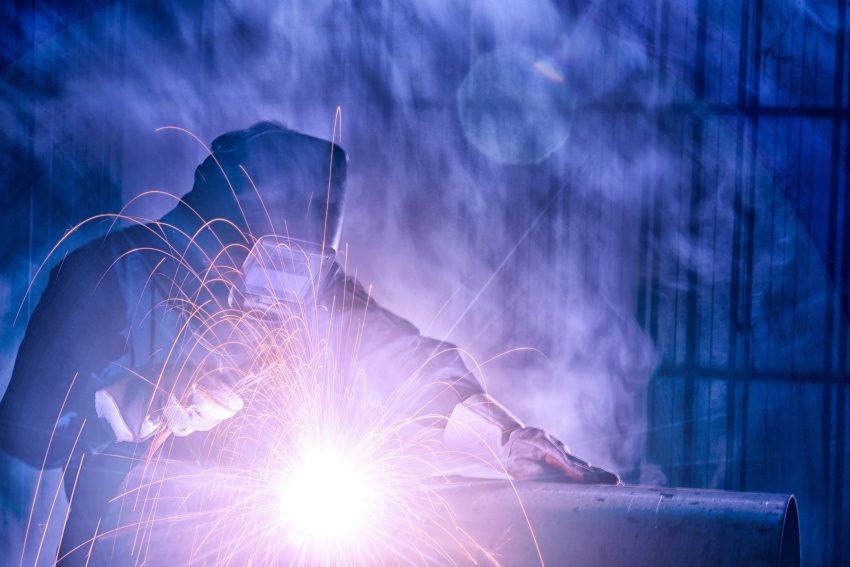
High-frequency resistance welding (HFRW) encompasses various resistance welding processes that utilize a high-frequency welding current to concentrate heat at specific locations for welding. This heat, generated through the electrical resistance of the workpiece to high-frequency currents, facilitates the fusion of metals, often accompanied by an applied upsetting force to achieve a forged weld. Primarily, HFRW finds its application in the production of seam-welded pipe and tube.
The Process of Induction Seam Welding
In induction seam welding, pipe or tube formation occurs from a metal strip in a continuous-roll forming mill, with the edges earmarked for welding slightly separated. Forge pressure rolls bring together the open edges of the pipe or tube into a V shape until they touch at the apex, where the weld forms. The weld point, situated at the center of the mill forge rolls, experiences the pressure necessary for forging the weld.
An induction coil, typically constructed from copper tubing or copper sheet with attached water-cooling tubes, encircles the tube (the workpiece) at a distance equivalent to 1 to 2 tube diameters ahead of the weld point. This distance termed the “vee length,” induces a circumferential current in the tube strip, closing as it travels down the edge of the V through the weld point and back to the portion of the tube under the induction coil. The high-frequency current predominantly flows along the edge of the weld V due to the proximity effect, wherein the current path at the surface of the workpiece is influenced by its proximity to its own return path.
The geometry of the weld V typically spans between 1 1/2 to 2 tube diameters in length, with an included angle ranging from 3 to 7 degrees. A suitable V angle is crucial to prevent arcing between edges or dispersion of heating, which may cause buckling. Adjustments in vee length and angle directly impact weld quality. Welding speed and power source levels are regulated to ensure both edges reach the welding or forge temperature at the weld point. Forge rolls then press the hot edges together, applying an upset force to complete the weld, extruding hot metal-containing impurities from the faying surfaces of the joint.
An impeder, usually made of a magnetic material like ferrite, is typically placed inside the tube, extending beyond the apex of the V and upstream of the induction coil. The impeder enhances the inductive reactance of the current path along the inside wall of the workpiece, reducing unwanted current flow and enhancing power transfer efficiency. Cooling of the impeder prevents it from exceeding its Curie temperature, where it loses its magnetic properties.
source: www.aws.org