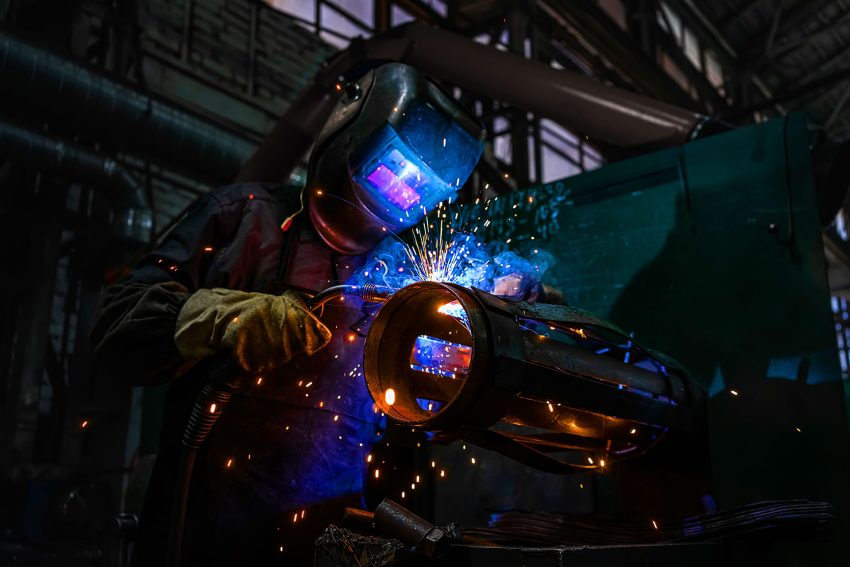
The selection of output current in SMAW encompasses more than a simple choice between alternating current (AC) and direct current (DC).
Shielded Metal Arc Welding (SMAW), commonly known as stick welding, stands as a cornerstone in the welding industry due to its versatility and widespread application. At its heart, SMAW relies on an electric circuit that transforms line power or fuel into heat, creating a welding arc. This article delves into the intricacies of SMAW output current, exploring the nuances between Alternating Current (AC) and Direct Current (DC), and how these choices profoundly impact your welding performance.
Understanding the Electrical Basics
SMAW’s flexibility allows for the use of either AC or DC power, each bringing its own set of advantages and limitations to the table. The choice between these current types isn’t just a matter of preference; it can significantly influence electrode performance and overall weld quality. As we navigate through the key considerations, you’ll gain insights into making informed decisions for your welding projects.
The AC vs. DC Debate: Pros and Cons
When it comes to welding at a distance from your power source, AC proves its worth. It experiences less voltage drop over long cables, making it the more efficient choice for remote welding jobs. However, welders must exercise caution when using AC cables, as coiling them can lead to substantial inductive losses, potentially compromising weld quality.
For precision work involving small-diameter electrodes and low welding currents, DC typically takes the lead. It provides better stability and arc characteristics, making it the preferred choice for delicate welding tasks that require finesse and control.
Arc initiation and stability present another point of comparison between AC and DC. Generally, DC offers easier arc striking, especially when working with smaller electrodes. AC, due to its cyclical nature, requires periodic arc reignition, which can present challenges in starting and maintaining a stable arc. This characteristic demands more skill and attention from the welder when using AC.
Maintaining a short arc length is crucial for achieving optimal weld properties, and DC excels in this area. It allows for better control of short arcs compared to AC, giving welders more precision in their work. However, it’s worth noting that electrodes with high iron powder content can help mitigate this advantage for AC welding, leveling the playing field in certain applications.
The phenomenon of arc blow, which is the unwanted deflection of the arc by magnetic forces, presents differently in AC and DC welding. With AC, arc blow is rarely an issue due to the rapidly reversing magnetic field. DC, especially when welding ferritic steels, can be more prone to arc blow problems, requiring welders to employ specific techniques to counteract this effect.
Positional Welding and Material Considerations
When it comes to out-of-position welding, such as vertical and overhead welds, DC slightly edges out AC due to its superior performance at lower amperages. This advantage allows for better control in challenging positions. However, it’s important to note that with the right electrodes and technique, AC can still produce satisfactory results in all positions, making it a viable option for diverse welding scenarios.
The thickness of the metal being welded also plays a role in the AC vs. DC decision. While both current types can handle a range of metal thicknesses, DC tends to produce better results on sheet metal. The enhanced arc stability of DC at low currents makes it particularly suitable for thin materials, allowing for more precise and controlled welds.
Mechanical properties of the weld are another crucial consideration. Welds made with Direct Current Electrode Positive (DCEP) generally exhibit superior mechanical properties, particularly in terms of weld metal toughness. This advantage stems from the ability to maintain a shorter arc with DCEP, resulting in fewer impurities from air contamination and consequently, a stronger weld.
Choosing the Right Power Source
Selecting the appropriate power source is paramount for successful SMAW operations. The ideal power source for SMAW is a constant-current type with at least a 60% duty cycle at maximum application current. This specification ensures consistent performance and reduces the risk of overheating during extended welding sessions. It’s worth noting that constant-voltage power sources are unsuitable for SMAW due to the difficulty in maintaining a constant arc length, which is critical for producing high-quality welds.
Conclusion: Tailoring Your Approach
The selection of the correct output current for your SMAW application involves careful consideration of various factors against your specific welding needs. Whether you opt for AC or DC will depend on your working conditions, material properties, and desired weld characteristics. By understanding these principles, you can ensure your SMAW output current is set correctly, paving the way for high-quality, efficient welds.
Mastering SMAW goes beyond simply choosing between AC and DC. It requires a deep understanding of how each option affects your welding process in different scenarios. With this knowledge, welders can make informed decisions that elevate their welding game and produce consistently excellent results. As you apply these insights to your welding projects, you’ll find yourself better equipped to tackle a wide range of welding challenges, ultimately improving your skills and the quality of your work.
Source : December 2022 Volume 101 Number 12 PG 67 “Output Current for SMAW”