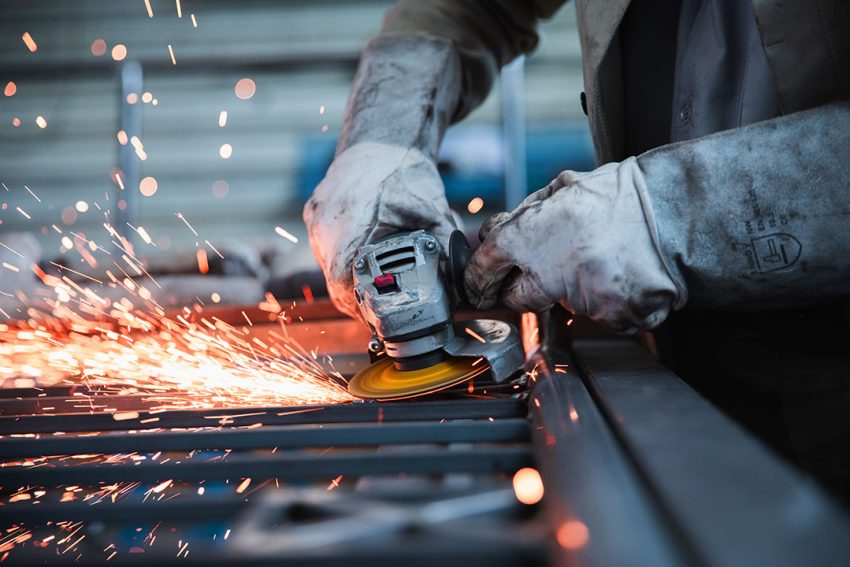
Bevelers are gaining popularity as a more precise and efficient alternative.
Weld preparation is a critical step in the welding process, directly impacting the quality and strength of the final product. While angle grinders have long been a staple in welders’ toolkits, bevelers are emerging as a superior alternative for precise and efficient weld preparation. This article explores the advantages of bevelers and why they’re becoming an essential tool for metal fabricators and welders.
The Limitations of Angle Grinders
Angle grinders are versatile tools used for grinding, cutting, cleaning, and polishing. However, their lack of precision in edge preparation can lead to uneven surfaces, excessive material removal, and heat-induced material property changes. These issues can potentially result in weaker welds due to oxidation. Additionally, it takes years of experience to achieve clean, straight cuts for weld preparation with an angle grinder.
Safety is another concern with angle grinders. They often produce hazardous dust and fumes, creating a potentially unsafe work environment. The production of flying sparks and the risk of respiratory health issues are significant drawbacks to consider.
The Beveler Advantage
Bevelers offer several advantages over angle grinders when it comes to weld preparation. They produce weld-ready bevels with minimal need for secondary operations, saving time and improving efficiency. Bevelers achieve more consistent, clean edges compared to angle grinders and are suitable for various materials including steel, stainless steel, aluminum, brass, copper, and plastic. They’re effective on diverse surfaces such as holes, cut-outs, radii, and straight, round, or curved contours.
From a safety perspective, bevelers address many concerns associated with angle grinders. They don’t produce flying sparks, instead creating metal chips that are easier to contain and clean up. This significantly reduces the risk of respiratory issues and creates a safer overall working environment.
Cost-Effectiveness of Bevelers
Despite the initial investment, bevelers can be more economical in the long run. Their increased efficiency and precision reduce the need for rework, while improved weld quality leads to fewer failures and repairs. Bevelers also require minimal skill to operate effectively, potentially reducing training costs and making them accessible to a wider range of workers.
Choosing the Right Beveler
When selecting a beveler, it’s important to consider factors such as size, portability (corded vs. cordless), and available accessories for specific applications. The reputation of the manufacturer and the durability of the tool are crucial for ensuring a good return on investment. It’s also worth looking for innovative features like booster and spring technology, which can significantly improve performance and user experience.
Advanced technologies in modern bevelers include booster technology, which absorbs and releases kinetic energy for smoother operation, and spring technology, which cushions rotational force for easier material penetration and reduced kickback. These features can make a significant difference in the quality and ease of weld preparation.
Conclusion
While angle grinders remain useful in welding workshops, bevelers offer significant advantages in weld preparation. By investing in a high-quality beveler, welders and metal fabricators can achieve superior results, improve safety, and potentially reduce long-term costs. As the industry evolves, embracing innovative tools like bevelers can give professionals a competitive edge in precision, efficiency, and overall weld quality. For any skilled metal fabricator or welder, adding a beveler to their toolkit could be a game-changing decision that improves both the quality of their work and their bottom line.