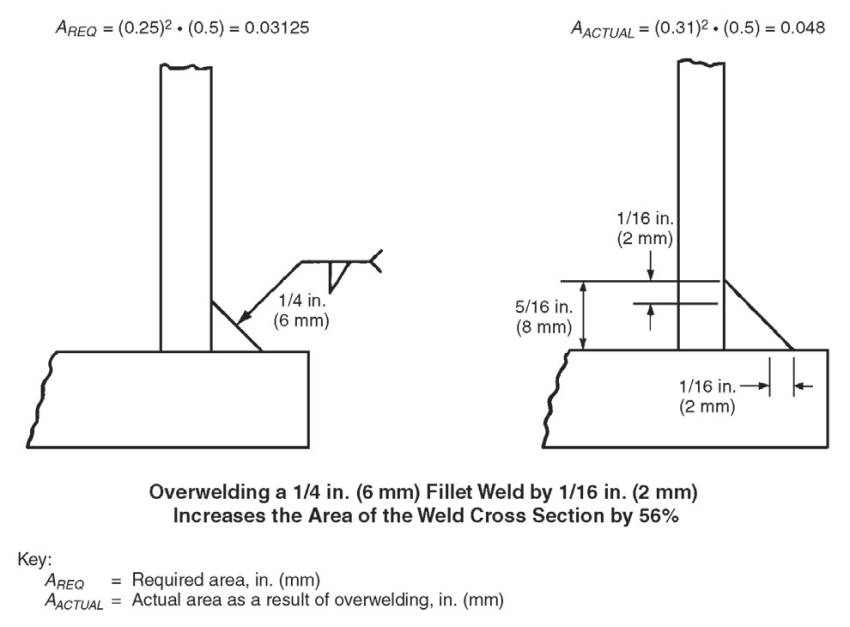
One of the most frustrating scenarios in a project occurs when costs have been estimated, orders have been received, and products have been manufactured, only to discover that the actual cost of the job exceeds the initial estimate. This situation becomes even more exasperating when no clear cause can be attributed to the cost overrun. Often, the problem arises from failing to identify all the factors influencing costs, especially those that are not directly related to material or labor expenses. Sometimes, costs are concealed within unanticipated operations. The following explores various factors that can impact overall costs.
Quality Considerations
Quality issues must be recognized as a factor in managing welding and cutting costs effectively. The cost of quality can be calculated and included in the cost estimate, provided that hidden steps or unnecessary operations are identified and evaluated. However, the cost of quality is not always immediately apparent. It may manifest in the scrap bin or in an unexpected repair job that occurs when a workpiece is not cut or welded according to specifications. It may be hidden in the inherent rework that occurs when manufacturing weldments that exceed the performance capabilities of the fabrication or welding equipment. A typical example of concealed quality costs would be weld joint preparation in which the oxyacetylene cut quality is so poor that extra grinding is required in a rework operation to bring the workpiece into compliance with dimension, tolerance, or surface finish requirements. Another example would be the welding of a multipass joint in which grinding is necessary to prevent incomplete fusion. Both the grinding and the metal removal and replacement require additional time and materials to complete the weld. The production department supervisor is usually aware of these conditions and takes appropriate corrective action.
Nevertheless, the lost time and additional labor and material may not be identified and could become a regular shop practice without the estimator’s knowledge. If the costs incurred in the additional procedures have not been factored into the cost estimate, the estimate will be inaccurate.
Excessive Welding
Excessive welding is another unforeseen cost. It typically results from inaccurate cutting and fitting, poor supervision, insufficient training (including on the proper use of measurement devices), or lack of confidence in the specified weld strength. Two joint configurations that often lead to excessive welding are complete or partial joint penetration welds in T-joints produced in the horizontal position and butt joints fabricated between plates of unequal thickness. Excessive welding significantly contributes to increased welding costs. As an example, the increase in weld cross-section resulting from excessive welding is shown in Fig. 1. Excessive welding also increases arc time and introduces opportunities for unnecessary defects that could have been prevented by stricter adherence to the specified weld size.
source: www.aws.org September 2023 Volume 102 Number 9 PG 63 “The Unforeseen Cost of Welding & Cutting”